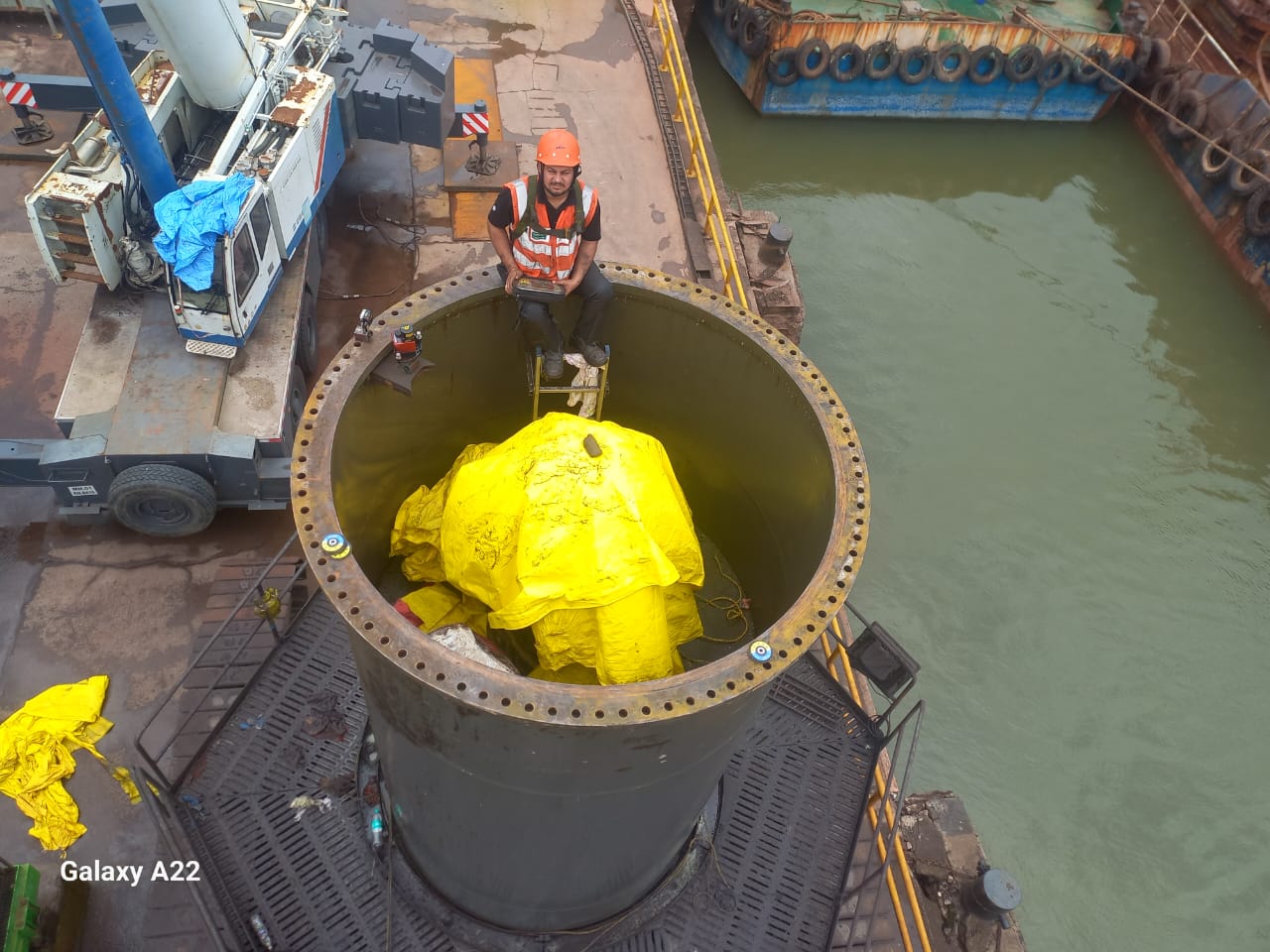
Shaft alignment is the method to align two or more shafts with each others to within a tolerated margin. In Surat Gujarat, where the manufacturing and processing sector is as powerful as ever, the need for quality shaft alignment services is on the increase. Shaft Alignment Services in Surat; these are vital for textile, chemical, power plant and engineering industries. This is because; even slight misalignments can cause severe process disturbances and economical losses.
Understanding Shaft Alignment
The alignment of two or more shafts so that they are co-linear; i.e in the same straight line, vertically and horizontally Shaft alignment is the process to align two or more shafts with each other to within a tolerated margin. Thus, it is a necessary part of maintenance and machinery. This is important for the smooth running of linked equipment including motors, pumps, compressors, gearboxes and turbines.
Perfect alignment avoids vibration; wear on bearings and seals and premature failure of couplings and other components. Mainstream methods such as Rakes and wheel gauges are very time consuming and of low ranging factor than digital devices. Nowadays, more advanced laser shaft alignment tools enable more precise, fast and repeatable processes.
Importance of Precision Alignment in Surat’s Industries
With Surat’s busy industrial phase, it is all of the more important that machinery keeps running efficiently. Misalignments can result in increased vibration levels, high failure rate and maintenance costs.
Shaft Alignment Services in Surat Gujarat Price
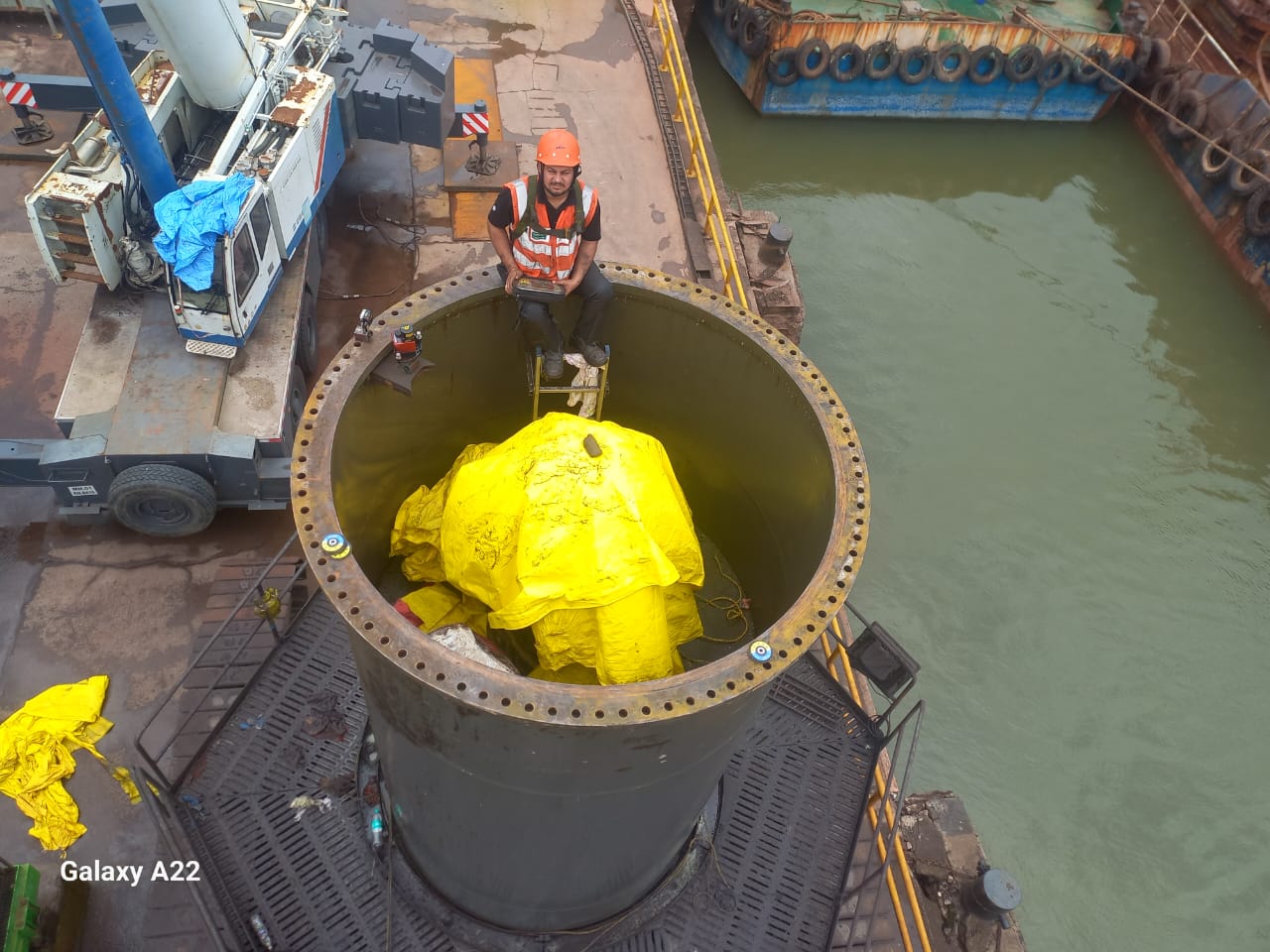
In textile mills and chemical plants for instance, a small misalignment can bring the production line to a halt and cause expensive down time. Companies in Surat can benefit from precision alignment by using Laser Shaft Alignment services, like as improve plant reliability, reduce maintenance costs, and lower overall plant operating costs. So, these advanced services can help companies in Surat to get 1 position.
More Uptime: Being perfectly aligned, there is low downtime of machine breakdowns. And, it increases continuous production and overall productivity.
Longer Component Life: Perfect alignment reduces the load exerted on bearings, seals, and couplings. Thus, this protects your equipment and makes for longer lasting components.
Reduced Energy Use: In line machines run more efficiently; so you’ll see a reduction in energy consumption and lower energy bills.
Lower Maintenance Costs: Less repair and fewer part replacements reduce maintenance costs and less downtime.
Enhanced Quality of Product: Reduced vibration and stable operation offer the better quality product which is less likely to have defects.
Laser Shaft Alignment: The Modern Solution
The laser shaft alignment has changed the way the job is done, it speed up, easier to do, can archive a reference of measurement. They leverage the latest in laser tech for a very accurate method of detecting and realigning shaft positions. It is possible with easy to use software that cleans up the user’s experience.
There are also systems that can measure and record up to five couplings at the same time, this can be useful on complex machine trains. 3D visualization, automatic data logging, and thermal growth compensation are some of the features that also contribute to improved accuracy and reliability.
Choose Shaft Alignment Service in Surat
Laser Tech Solution & Services – Experienced Shaft Alignment services are available through Surat’s well established industrial sector. Top businesses offer onsite service which involves trained technicians armed with the latest laser alignment tools.
These professional assess alignment requirements, make sure installation and foundation is carried out correctly. A broad offering of services are applicable to various types of equipment such as motors, pumps, gearboxes, compressors and turbines. This means; every critical rotating asset can be in its best condition when the peak of performance is required.